What is SMD? A Deep Dive into Surface-Mounted Devices
In the world of modern electronics, SMD (Surface-Mounted Devices) have become a cornerstone of manufacturing, particularly in the field of LED display technology. The rise of SMD components has revolutionized the way electronic circuits are designed and manufactured, making them smaller, more efficient, and cost-effective. But what exactly is SMD, and why is it so crucial in the context of LED displays?
Table of Contents
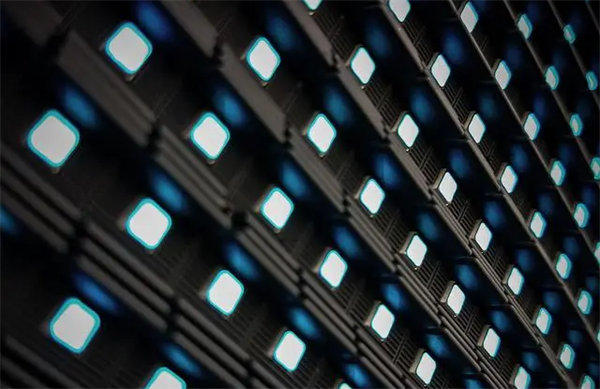
What is SMD?
SMD stands for Surface-Mounted Device, which refers to a method of mounting electronic components directly onto the surface of a printed circuit board (PCB) rather than inserting them through holes in the board, as is done in traditional through-hole technology (THT). SMDs are placed onto the surface of the PCB using advanced machines that solder them in place, providing a more compact, reliable, and efficient design.
Unlike through-hole components, which require more space and extensive manual handling, SMD components are much smaller, offering greater flexibility in circuit design. This allows manufacturers to create more intricate and high-performance electronic devices, such as LED displays, that are both lighter and more durable.
The History and Evolution of SMD Technology
The concept of surface-mount technology (SMT) began to emerge in the late 1960s and early 1970s, as the electronics industry sought ways to reduce the size and cost of electronic products. SMT provided a more efficient and scalable solution to the growing demand for smaller, more powerful devices.
In the early days, SMT was largely used for simple components like resistors and capacitors. However, as the technology matured, it quickly became the preferred method for all types of components, from microprocessors to LEDs. By the late 1980s, SMT had become the standard in electronics manufacturing, particularly for industries like telecommunications, automotive, and consumer electronics.
The Key Features of SMD
SMDs come in a variety of shapes and sizes, but they share some common features that set them apart from traditional components:
- Small Size: SMDs are significantly smaller than through-hole components, allowing for greater miniaturization of devices and more compact PCB layouts.
- High Density: Because SMDs are mounted directly on the surface of the PCB, they allow for a much higher density of components on the board, improving performance and reducing the space required.
- Automated Placement: SMD components are placed on the PCB using automated machinery, which increases the speed and precision of assembly, reduces human error, and lowers labor costs.
- Improved Durability: The solder joints used for SMDs are generally more reliable than through-hole solder joints, which improves the overall durability and lifespan of the product.
The Role of SMD in LED Display Technology
LED displays have become a ubiquitous technology, seen in everything from smartphones and televisions to billboards and digital signage. The integration of SMD technology in LED displays has dramatically improved their efficiency, brightness, durability, and overall performance.
How SMD Improves LED Displays
Smaller, Brighter, and More Efficient: One of the main benefits of using SMD technology in LED displays is the ability to produce smaller, more compact designs that offer higher brightness levels while consuming less energy. The small size of SMD LEDs allows manufacturers to create high-resolution displays with greater pixel density, resulting in sharper images and more vibrant colors.
Cost-Effectiveness: SMD LEDs can be produced in large quantities using automated processes, which significantly reduces manufacturing costs. This makes LED displays more affordable and accessible for a wide range of applications, from consumer electronics to commercial advertising.
Enhanced Durability: The integration of SMD LEDs into displays increases their resistance to physical stress, such as vibrations and impacts. The smaller size and better mounting technique help reduce the likelihood of component failure, extending the lifespan of the display.
Higher Performance and Reliability: SMD LEDs are often more reliable than traditional LEDs, as the surface-mount technology reduces the number of physical connections and ensures a stronger bond between the LED chip and the PCB.
SMD LED Displays vs. Traditional LED Displays
Traditional LED displays, often referred to as “through-hole” displays, use larger, bulkier components that require more space and are more prone to failure due to weaker connections. In contrast, SMD LED displays are more compact, efficient, and reliable, making them ideal for modern applications where space is limited, and high performance is a priority.
The Benefits of SMD Technology for LED Displays
1. Improved Viewing Angle and Brightness
One of the key benefits of SMD technology in LED displays is its ability to improve the viewing angle and brightness of the display. SMD LEDs emit light in a more uniform and directed way, which means that images are clearer and brighter even from off angles. This makes SMD LED displays ideal for large-scale outdoor billboards or digital signage, where visibility from various distances and angles is crucial.
2. Better Thermal Management
Heat management is a critical issue in any electronic device, especially in LED displays. SMD technology improves thermal dissipation by providing a more efficient surface area for heat to escape. This is important for ensuring the longevity of the LED components and maintaining their brightness over time.
3. More Design Flexibility
SMD LEDs offer greater flexibility in design, allowing manufacturers to create displays with unique shapes, sizes, and configurations. This is particularly beneficial for applications in architecture, entertainment, and creative industries, where unconventional display designs are often required.
The Manufacturing Process of SMD LED Displays
Step 1: Component Placement
The process begins with the preparation of the PCB, which is typically a thin, flat surface that holds the electronic components. In the case of SMD LED displays, a pick-and-place machine is used to place thousands of tiny LED components on the surface of the PCB. The machine uses precise robotic arms to position the SMD LEDs accurately on the board.
Step 2: Soldering
Once the SMD LEDs are placed, the next step is to solder them onto the PCB. This is done using a reflow soldering process, in which the board is heated to a specific temperature that melts the solder and secures the components in place. This process ensures strong, reliable connections between the LEDs and the PCB.
Step 3: Testing and Inspection
After the soldering process, the PCB undergoes a series of quality control tests to ensure that all the LEDs are functioning correctly. This includes testing the brightness, color accuracy, and functionality of each individual LED. Automated optical inspection (AOI) machines are often used to identify any defects or issues with the components.
Step 4: Final Assembly
Once the LED array has passed inspection, it is assembled into its final form, whether that be a television screen, outdoor billboard, or digital signage unit. The display is then subjected to further testing to ensure that it meets all performance standards before being shipped out.
The Future of SMD in LED Displays
As LED technology continues to evolve, SMD will play an increasingly important role. The ongoing demand for high-resolution, energy-efficient displays means that manufacturers will continue to push the boundaries of SMD technology, developing new innovations that further enhance performance and reduce costs.
Emerging Trends in SMD LED Displays
Micro-LED Technology: Micro-LED is an emerging technology that builds on the principles of SMD, but with even smaller LEDs that can be used to create ultra-high-resolution displays. Micro-LED displays offer superior brightness, contrast, and color accuracy, and are expected to become a key player in the future of display technology.
Flexible SMD LED Displays: The development of flexible, bendable displays is another trend that is likely to shape the future of SMD LED technology. Flexible LED screens are already being used in a variety of applications, from curved TVs to wearable devices.
OLED vs. SMD LED Displays: OLED (Organic Light Emitting Diodes) are often seen as a competitor to traditional SMD LEDs in display technology. While OLED offers better contrast and color accuracy, SMD LED displays still have advantages in terms of durability, cost, and scalability.
Conclusion: Why SMD is Essential for the Future of LED Displays
SMD technology has revolutionized the electronics industry, particularly in the realm of LED displays. Its ability to create smaller, more efficient, and reliable components has made it an essential technology for modern devices. As demand for high-performance displays continues to grow, SMD technology will remain a driving force behind the evolution of LED displays, paving the way for even more advanced, energy-efficient, and cost-effective solutions in the years to come.
Contact us today to explore how our professional LED displays can transform your bars’visual environment!