Understanding LED Display Packaging Technologies: SMD, COB, and More
Table of Contents
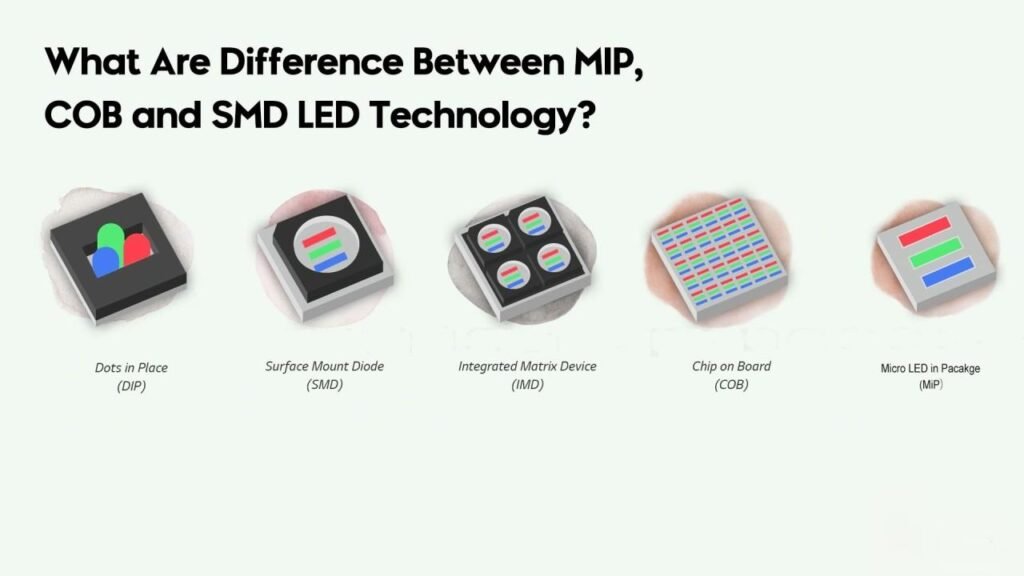
When it comes to setting up your LED display, choosing the right packaging technology is crucial. From indoor displays to large outdoor screens, the performance, lifespan, and image quality depend on the type of packaging used to integrate the LED chips with the circuit board. In this article, we’ll break down the most common LED packaging technologies—DIP, SMD, GOB, COB, IMD, MIP, and COG—and help you figure out which is the best fit for your needs, especially in small-pitch displays.
What is LED Display Packaging?
LED display packaging refers to how the individual LED chips are mounted, protected, and connected to the driving electronics. A good packaging solution not only ensures the LED’s longevity but also improves the display’s brightness, clarity, and overall performance. Packaging technology plays a significant role in both the visual quality and the physical durability of the display.
Whether you’re designing a high-definition screen for a retail store or a large outdoor billboard, LED packaging technology affects everything from the display’s reliability to its ability to work in various environmental conditions.
Types of LED Packaging Technologies You Should Know About
There are several packaging technologies used in LED displays, and each comes with its unique advantages and challenges. Below, we’ll take a closer look at DIP, SMD, IMD, GOB, COB, MIP, and COG technologies, explaining their features, benefits, and possible limitations.
DIP (Dual In-line Package) – The Traditional Option
If you’ve been in the LED industry for some time, you’ve probably encountered DIP packaging, especially in older or larger outdoor LED displays. It involves the mounting of the LED chips using leads or pins that are inserted into holes in a circuit board.
Advantages of DIP:
- Cost-effective: DIP is one of the most affordable packaging methods.
- Rugged and durable: It offers strong protection against weather elements, making it perfect for outdoor advertising.
- Mature technology: This well-established method is reliable for larger displays with lower pixel densities.
Disadvantages of DIP:
- Larger in size: DIP is bulky and not ideal for high-resolution displays.
- Lower pixel density: The technology is outdated for finer displays, especially in small-pitch applications.
- Heat management issues: This packaging has higher heat dissipation challenges compared to newer methods.
SMD (Surface-Mounted Device) – The Industry Standard for Indoor Displays
SMD is the most widely used packaging technology today, especially for indoor LED displays. In SMD, the LEDs are mounted directly onto the surface of the PCB without the need for leads, resulting in a more compact design.
Advantages of SMD:
- High brightness: SMD LED displays are capable of producing vivid colors and superior brightness.
- Slim and sleek: Perfect for smaller, more compact displays, especially for small-pitch LED applications.
- Better heat dissipation: SMD technology generally offers better thermal management than DIP.
- Wide viewing angle: It provides great visibility from different angles.
Disadvantages of SMD:
- Higher cost: Compared to DIP, SMD is more expensive due to more advanced manufacturing techniques.
- Complexity in production: The precision required in SMD assembly increases the manufacturing complexity and cost.
IMD (Integrated Molding Device) – The Protective Packaging
IMD is a more advanced LED packaging method where the LED chip and its driving circuit are encapsulated in a single module. The primary benefit of IMD is its ability to enhance the protection and reliability of the display.
Advantages of IMD:
- Increased durability: IMD packaging offers excellent protection from moisture and dust, making it ideal for harsh environments.
- Compact design: It allows for higher pixel densities and more compact displays.
- Enhanced reliability: Because of its sealed nature, IMD displays tend to have a longer lifespan.
Disadvantages of IMD:
- Higher cost: The added protection and compactness come at a price.
- Complicated manufacturing: IMD involves advanced molding processes, making it harder to produce and more expensive.
GOB (Glue on Board) – A Newer, Protective Option
GOB packaging technology has gained traction due to its excellent protection features. It uses a glue-based method to mount the LED chips onto the board, followed by a protective resin to safeguard the components.
Advantages of GOB:
- Improved durability: GOB offers exceptional resistance to moisture, vibrations, and external impacts.
- Lower light loss: GOB ensures that light loss is minimized during the mounting process, which improves the display quality.
- Enhanced reliability: It provides long-term durability, especially in outdoor environments.
Disadvantages of GOB:
- Thermal challenges: GOB still faces challenges with heat dissipation, though it’s better than DIP.
- Material quality: The effectiveness of the protective resin used in GOB is dependent on the material’s quality.
COB (Chip on Board) – High-Density, High-Performance Display
COB packaging places the LED chips directly onto the circuit board, eliminating the need for traditional LED encapsulation. This results in a more efficient, space-saving design that can accommodate high-density pixel configurations.
Advantages of COB:
- High brightness and resolution: COB allows for higher pixel density and better brightness, ideal for high-definition applications.
- Improved thermal management: It offers better heat dissipation compared to GOB and DIP.
- Compact and reliable: Ideal for both small-pitch LED displays and large-scale screens.
Disadvantages of COB:
- Higher cost: COB’s advanced technology comes with a premium price tag.
- Complicated assembly: The manufacturing process is intricate and requires precise equipment.
MIP (Matrix Integrated Package) – High Pixel Density for Ultra-HD
MIP technology is designed for displays requiring ultra-high pixel densities. It integrates multiple LED chips in a matrix, which makes it perfect for applications requiring extremely fine details.
Advantages of MIP:
- Extremely high pixel density: MIP excels in delivering ultra-high-definition (UHD) displays with excellent color accuracy.
- Better visual performance: The higher density translates into sharper, more vibrant images, perfect for small-pitch applications.
- Great for close viewing distances: Perfect for applications where viewers are very close to the screen.
Disadvantages of MIP:
- Complexity: MIP requires precise and intricate assembly, leading to higher production costs.
- Heat management: Like COB, MIP displays need careful thermal management to maintain performance.
COG (Chip on Glass) – A Unique Solution for Outdoor Applications
COG technology involves mounting LED chips directly onto glass substrates, making it ideal for outdoor LED displays due to its exceptional durability and resistance to the elements.
Advantages of COG:
- Exceptional brightness: Perfect for high-brightness, large outdoor screens.
- Durable: Resistant to environmental factors like moisture, dust, and extreme temperatures.
- Reduced light loss: This method reduces light loss, ensuring better display performance.
Disadvantages of COG:
- Heat dissipation concerns: Managing heat is more challenging with COG compared to other methods like SMD or COB.
- Expensive: COG technology can be more costly due to the complexity of the process.
Different LED Display Packaging Technology Advantages and Disadvantages Comparison
Technology | Advantages | Disadvantages |
---|---|---|
DIP (Dual In-line Package) | – Cost-effective – Rugged, ideal for outdoor use – Well-established, reliable | – Large size, not suitable for high-resolution – Lower pixel density – Poor thermal management |
SMD (Surface-Mounted Device) | – High brightness and resolution – Thin, compact design – Good heat dissipation – Wide viewing angle | – Higher production cost – Manufacturing complexity |
IMD (Integrated Molding Device) | – High pixel density – Excellent protection from dust, moisture, and external elements – Compact and durable | – Expensive to produce – Complex manufacturing process |
GOB (Glue on Board) | – Excellent durability, waterproof, and shockproof – Reduces light loss – Long-lasting | – Heat dissipation challenges – Resin quality affects performance |
COB (Chip on Board) | – High brightness and clarity – Excellent heat dissipation – Compact, ideal for small-pitch displays – More reliable and robust | – Expensive due to advanced technology – Complex assembly process |
MIP (Matrix Integrated Package) | – Ultra-high pixel density – Exceptional color and image quality – Ideal for small-pitch, ultra-HD applications | – High production cost – Heat management is a challenge |
COG (Chip on Glass) | – Excellent brightness for outdoor displays – High durability, resistant to environmental factors – Minimal light loss | – Thermal dissipation concerns – Higher production cost – Complex manufacturing |
How to Choose the Right LED Display Packaging on Your Small Fine Pixels LED Video Wall?
Comparison of Mainstream Direct-View LED Technologies for Small-Pitch Applications
Packaging Technology | IMD | MiP | COB | COG |
---|---|---|---|---|
Pixel Pitch | P0.6-1.5 | P0.3-1.25 | P0.6-1.5 | P0.05-1.25 |
Suitable Process | SMT | SMT/DB+GOB | DB | Mass Transfer |
Substrate | PCB | PCB/Glass | PCB | Glass |
Cost | High | Low | High | Very High |
Complexity | Low | Medium | High | Extremely High |
Drawbacks | – Difficult to achieve small-pitch displays – Structure is relatively weak, affecting reliability | – High precision required for small-pitch – Color uniformity issues, poor image quality | – Higher cost and complex assembly – Poor color consistency and reliability | – Extremely high cost – Not fully matured technology, challenges in mass production |
Key Insights for Small-Pitch Applications:
IMD (Integrated Molding Device): Suitable for small-pitch displays with pixel pitches between P0.6 to P1.5. It provides a lower-cost solution with a relatively simple manufacturing process. However, achieving high precision in small-pitch configurations can be difficult, and its structure may be weaker, which could affect the display’s reliability and performance over time.
MiP (Matrix Integrated Package): Works well with P0.3 to P1.25 pixel pitches and provides a low-cost solution. However, this technology has a medium level of complexity. High precision is required for small-pitch applications, and color uniformity and image quality may suffer, which makes it less ideal for high-performance, ultra-clear displays.
COB (Chip on Board): Best for P0.6 to P1.5 pixel pitches, with a high manufacturing complexity. It is known for providing excellent brightness, clarity, and heat dissipation, making it ideal for small-pitch displays. However, the high cost of COB technology and issues with color consistency and reliability could be limitations for some projects.
COG (Chip on Glass): Can work with pixel pitches as fine as P0.05 to P1.25, offering outstanding display brightness for outdoor and high-performance applications. However, COG technology has a very high cost and is still not fully mature. Challenges with mass production, color uniformity, and overall consistency need to be addressed for broader usage.
How to Choosing the Right Packaging for Your Small-Pitch LED Display
If you’re working on a small-pitch LED display, it’s essential to choose a packaging technology that offers high resolution, excellent heat management, and durability. SMD and COB are the best options for this purpose, with COB being particularly ideal for high-density, high-quality displays that demand optimal performance.
MIP technology can be an excellent choice for ultra-high-definition applications that require superior image quality. For outdoor applications, GOB and COG are also great options, providing enhanced durability and resistance to the elements.
For small-pitch LED displays, COB and MiP stand out as the top choices. COB provides a high level of performance with excellent brightness and clarity, especially for higher-end displays. MiP, on the other hand, offers a cost-effective solution but may fall short in terms of color uniformity and precision.
If budget is a priority and the project demands high performance with relatively low complexity, IMD might be a viable option, although it comes with its own limitations. COG technology, while offering the best potential for ultra-high-definition displays, still faces challenges and remains costly for many small-pitch applications.
Conclusion
In the ever-evolving world of LED display technologies, the right packaging choice is vital for achieving the best performance, durability,
and cost-effectiveness. By understanding the unique strengths and challenges of DIP, SMD, GOB, COB, IMD, MIP, and COG, you’ll be equipped to make the right decision for your display needs.
Whether you’re setting up an indoor small-pitch display or a large outdoor billboard, understanding LED packaging technologies is crucial to optimizing your display’s performance.
Contact us today to explore how our professional LED displays can transform your bars’visual environment!